Waste treatment boosts pig farming sustainability
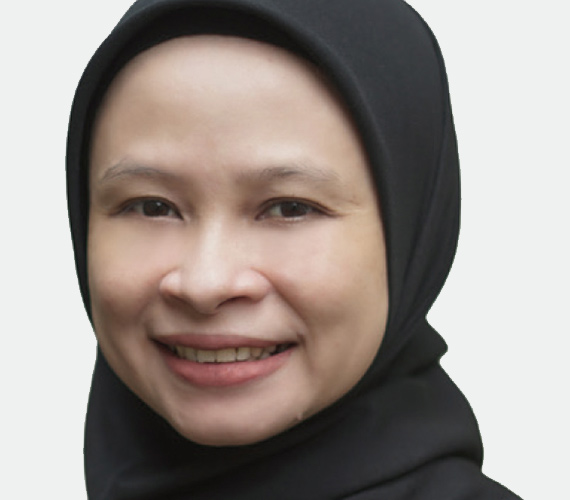
The clamor for technologies to manage pig waste and produce alternative energy simultaneously is increasing. The goal is not only to save on energy costs but to lower carbon footprint and make operations more sustainable. MELIYANA looks at currently available technologies to achieve these.
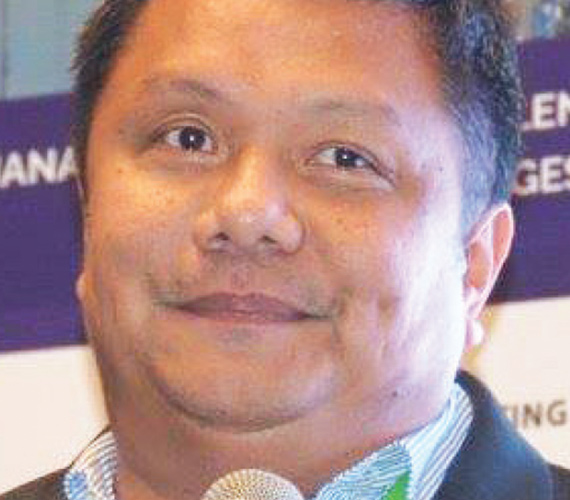
Pig waste is a problem because of its high organic load, measured in terms of chemical oxygen demands (COD) and biological oxygen demand (BOD).
“Releasing high organic load to rivers and other bodies of water will kill most aquatic life. It will rob the water of its oxygen content and will suffocate fish and other living things,” Nervy Santiago, VP for Technology and Innovation of the Asia Pacific Biogas Alliance, explained to Asian Pork Magazine.ig waste is a problem because of its high organic load, measured in terms of chemical oxygen demands (COD) and biological oxygen demand (BOD).
Ammonia, hydrogen sulfide, and nitrous amines result from the breakdown of animal manure; the more manure, the more substrates to produce these gasses.
“If you remove the manure immediately, then you remove the real source of these gasses. In tropical areas, a bio-methanation system manages pig waste and also produces power at the same time.
“The system provides the farm with readily available space to transfer the pig waste and prevent build-up in the barns,” Dr Santiago said.
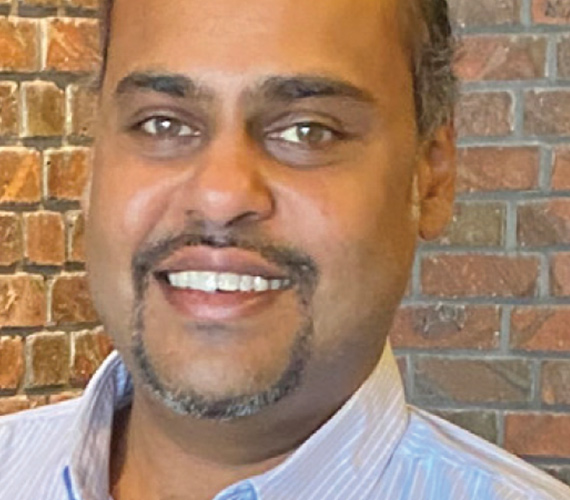
Opportunity in waste
Devan Krishnan, Product Sales Manager (Climate) at Big Dutchman (BD) Asia, explained that waste is only a problem if not managed properly. “We can turn this problem into profit for the farmer. Pig waste is a resource that can be turned into fertilizer that can be sold. The market demand for compost is rising, and we see prices increasing throughout Southeast Asia,” he told Asian Pork Magazine.
Ammonia emissions from pig sheds mainly result from ammonium volatilization of waste sludge. This is why BD’s environmental solutions team works closely with its sales channels across Asia.
“We design a complete solution that includes environmentally controlled sheds with automatic manure handling to ensure optimum environmental conditions and that the manure is removed from the sheds as fast as possible and treated properly,” explained Mr Devan.
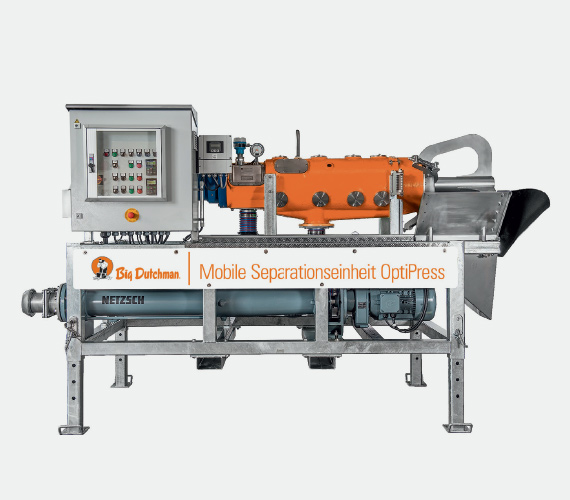
Commons solutions
The usual solutions for waste are solid-liquid separation, biogas, composting, ponding treatment, evaporation, and chemical treatments.
In Southeast Asia, it is common for producers to have some form of air treatment, achieved through either rudimentary catchments or evaporation ponds to high-end separators and biogas plants.
“Currently, not many companies are adopting these technologies, however as regulations become stricter, these environmental solutions will become key to pig farms,” he said.
Separating solid and liquid waste
Slurry can be separated using a screw press separator.
Big Dutchman offers a compact screw press called the OptiPress. This system can handle a large volume of slurry and achieve a higher level of dryness in separated solids.
For further treatment, it integrated the screw press with the slurry drying tunnel called the OptiSec Porco. This technology utilizes the warm air from the barn to air-dry the slurry and evaporate the separated liquid simultaneously.
This liquid is then sprayed onto the manure, resulting in pre-dried manure with a high nutrient value that could be used as organic fertilizer or further composted.
Big Dutchman also offers a compact filtration unit called the Memfis, which integrates OptiPress, sedimentation, and ultrafiltration units to treat the separated liquid fraction.
“At the end of the process, we will have separated solids for composting and filtrate with low nutrient content, which can be applied as liquid fertilizer,” Mr Devan said.
Last but not least, the pre-dried solids can be composted by using Big Dutchman’s CompoTower – a vertical enclosed composter. This provides an optimal environment for microorganisms to effectively degrade the organic matter in the manure to produce high-quality, pathogen-free compost.
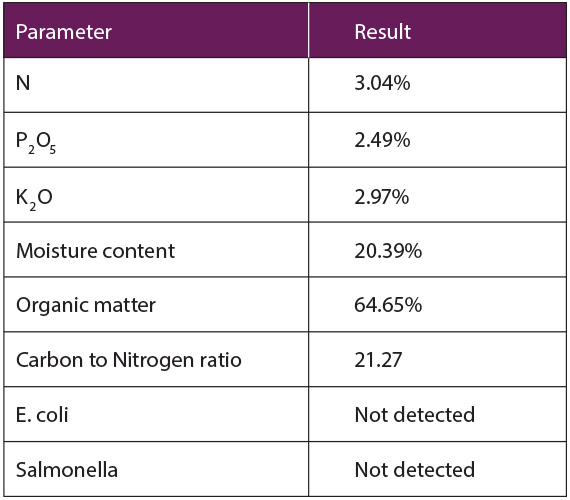
Bio-methanation
Meanwhile, Dr Santiago explained that with bio-methanation, liquid and solid wastes need not be separated, but only the inorganic and organic fractions. The system will digest the organic fraction anaerobically, naturally producing methane gas that can be captured and converted to heat and/ or electricity.
“Anaerobic digestion is just composting pig waste without oxygen. The beauty of the system is that it will decrease the pollution load of the wastewater while at the same time producing energy,” he explained.
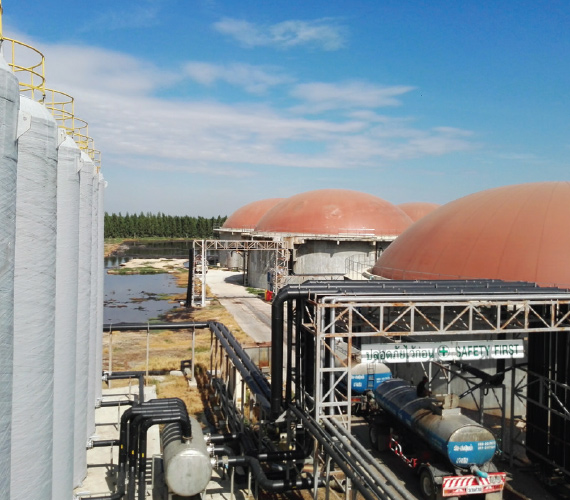
Investment costs
Most progressive farms will see the system's value because they have a long-term vision. However, Dr Santiago remarked that many farms tend to look at ‘cheap’ solutions that do not work.
“We've also seen several farms that have been fooled by ‘designers’ who just downloaded plans on the internet but have no idea how the system works. These are the farms we are trying to help out now,” he said.
He added that it is time to stop referring to manure as ‘waste’ since it is a valuable resource that should be recycled, reused, and returned into the production loop.
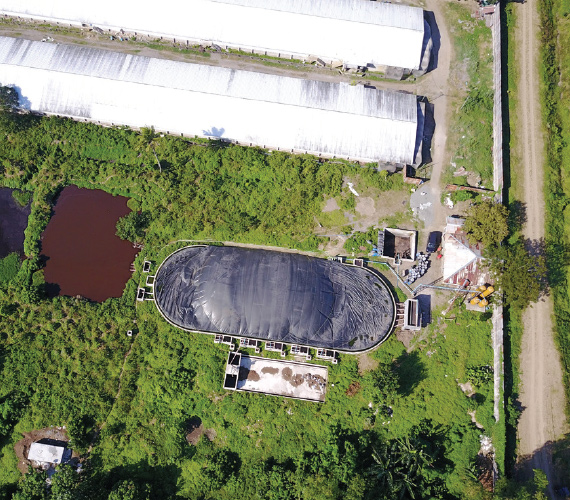
“The proper term is resource recovery, not waste management. Many farms now are trying to reduce carbon footprint and mitigate climate change by recovering this resource,” he said.
Dr Santiago explained that the system cost depends on its complexity. The bigger the system, the better to take advantage of economies of scale. The bigger the farm, the bigger the anaerobic digester, the main bio-methanation component, needed.
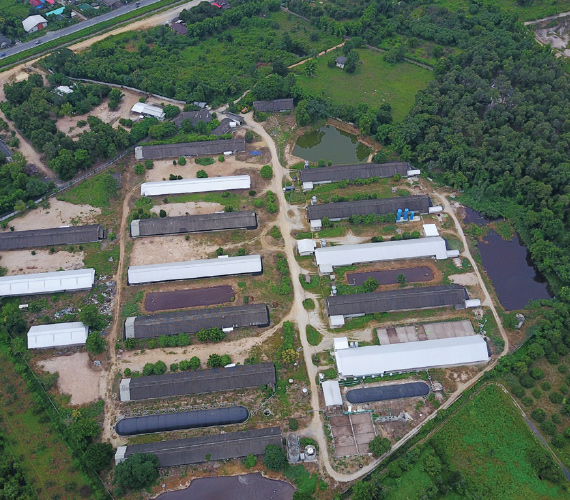
“In a country without winter, it is around USD 100-150/cubic meter of digester space,” he said. “We have done simulations all around Asia and the break-even point we are seeing is around 50 sows and higher if you want to produce electricity.
“A farm with fewer than 50 sows can implement a bio-methanation system just to treat waste and capture gas for farm cooking.”
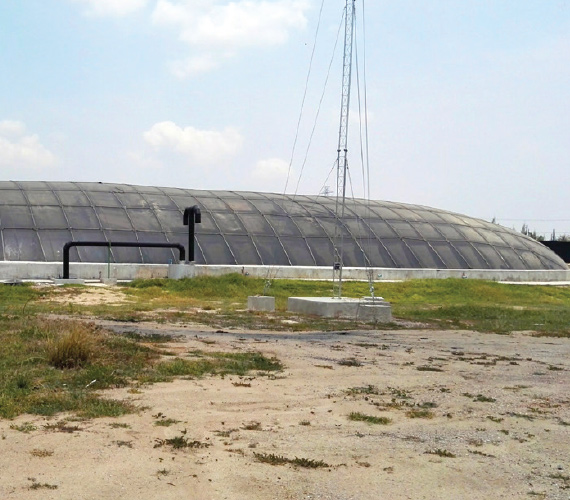
Mr Devan agrees that quantifying the cost of waste treatment is difficult since it depends on local guidelines, treatment approaches or requirements, farm capacity, and farm location.
“Our solutions are designed based on the customers and local guidelines for waste treatment. All our systems are flexible and modular, so they are competitive in terms of initial investment value and at a later stage, add on additional technologies for further treatment,” he said.
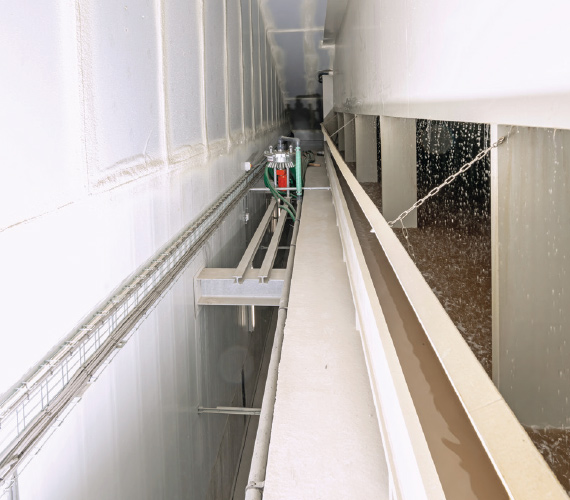
Good demand
Inquiries for waste treatment solutions at Big Dutchman have been increasing annually in the past five years. Consumers are influencing businesses and driving the trend, buying more fair trade items to ensure farming methods support sustainable environmental practices and social justice.
“Our customers and governments realize the necessity of environmental practices and the potential of the organic fertilizer business that can turn [manure] into profits,” Mr Devan said.
“In some markets with environmental legislations and good demand and price for organic fertilizers, waste treatment solutions can have a return on investment in as short as three years,” he explained.
Technology trends
Technological developments will always trend toward helping farmers generate income and greater profits that will encourage bigger initial investments for environmental solutions.
For its part, Big Dutchman is not only concentrating on downstream solutions such as the production of organic fertilizer but also upstream technologies that would improve the handling of manure inside the barn.
One such technology is the Havito concept, a smart barn with solid flooring for climate-friendly, sustainable piglet rearing and finishing. It separates the collection of feces and urine with a specially designed pig toilet, which means no more slurry generation.
“Manure treatment becomes easier and highly effective as there are virtually no ammonia emissions in Havito concept barns,” said Mr Devan.
For waste recovery, Big Dutchman notes that the trend is to retain as many nutrients as possible in the fertilizers while being pathogen-free, and hygienic.
Technologies to treat and process pig wastes will keep improving over time. The goal is to make them more cost-competitive while being more sustainable with a smaller carbon footprint compared to conventional treatment systems.