Asia: Big Dutchman steps up on automation as poultry industry consolidates
Recent changes in livestock production have forced businesses to consolidate quickly. Janjaap van der Mark of Big Dutchman tells HA THU that automation is key to helping farmers adapt to that.
Published with kind permission of Asian Poultry
Two pandemics have forced the landscape to change in livestock production in the last year, causing disruption to supply chains.
While the pandemic has caused severe price drops across essential food industries, African swine fever has caused pig populations to dwindle significantly. “ This dual impact and other diseases have forced producers to turn professional and modernize to reduce risks and increase efficiency. Consolidation is the inevitable consequence,” said Janjaap van der Mark, Big Dutchman’s Joint Managing Director and Director of Business Development in Asia.
While the entire livestock industry is undergoing major changes, one thing that remains unchanged is the importance of poultry. “The poultry industry still plays an important role in providing food. The pandemic has created an extra dimension in that countries are now becoming more self-sustainable in production,” Mr Van der Mark told Asian Poultry Magazine.
“Consolidation in Vietnam’s poultry industry has contributed to Big Dutchman’s growth in the past year,” said Mr Van Der Mark, adding that its poultry equipment business now accounts for nearly 10% of the company’s growth there.
At the same time, ASF has prompted pig breeders, including some large producers, to switch to poultry farming
“Consolidation has made small farms bigger and more professional. In this market, we have seen investments grow in automation and infrastructure, leading to a sharp rise in mid and large-sized farms.”
In addition to white chicken, a segment that has been industrialized for a while, Mr Van der Mark said he also sees strong growth in colored chicken and duck, which are still heavily dependent on traditional production methods.
“The production of colored chickens, laying ducks and broiler ducks is moving towards modern, industrial farming. This trend will only get stronger,” he said.
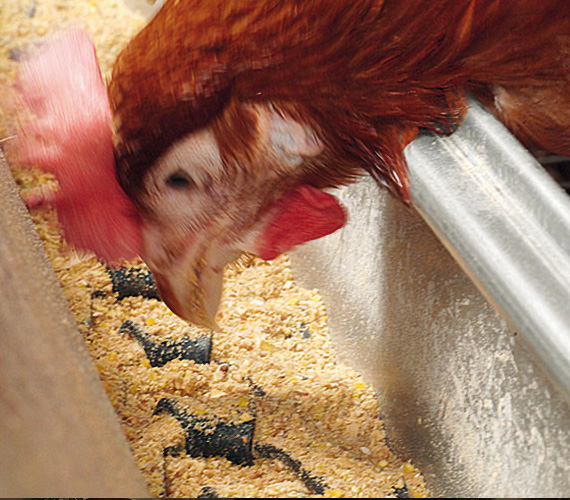
Automated solutions
Small-scale farming accounts for about two-thirds of Vietnam’s poultry industry. At these farms, animal husbandry knowhow is low and investment is at a minimum.
“These farms must quickly adapt to stay in existence, and automation is the inevitable solution. Automation increases scalability, thereby reducing the relative cost per animal,” he said.
To familiarize farmers with new technology, Big Dutchman provides simplified equipment and training to operate it. Its automated solutions are modular and suitable for a wide range of farm sizes.
“This allows farms to gradually grow bigger by applying capital investment in an efficient way. Larger farms just need to have more modules,” said Mr Van der Mark.
The upgrading of infrastructure helps farmers reduce production costs and increase efficiency.
“Automation helps reduce labor cost, limits the risks of human mistakes and spread of diseases,” he added.
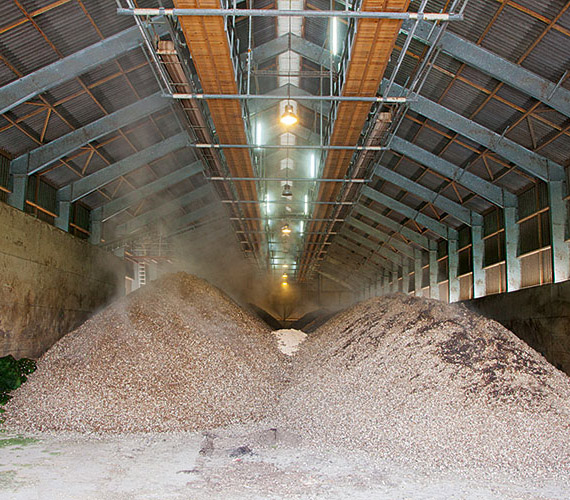
Turning waste into money
Big Dutchman is taking into consideration how consolidating production will inevitably lead to a heavier load on the environment.
In Vietnam, poultry farms sell wet manure to rubber and perennial fruit farms. However, fruit trees are seasonally fertilized. “It’s a problem in the off-season, when fruit farms stop buying the manure,” said Mr Van der Mark.
In addition, using and transporting wet manure presents the risk of disease spread and environmental pollution.
To solve this, Vietnam’s government encourages farms to apply waste treatment solutions to produce organic fertilizers. “This approach will bring benefits to the environment, reducing diseases and increasing livestock efficiency,” said the Minister of Agriculture and Rural Development, Nguyen Xuan Cuong.
Understanding this problem, Big Dutchman spent years researching ways to provide farmers with sustainable solutions that bring favorable investment returns within a short period. It recently started introducing fully automatic waste treatment and fertilizer production systems to farmers across Asia.
“The composting system gets rid of manure waste and dries it. Drying the manure is beneficial in terms of storage and gives it a longer life.
The system can turn dried manure into organic fertilizer, which can be pelletized and sold as a by-product,” said Mr Van Der Mark.
This system has three steps. The first involves collecting wet manure which is dried in a tunnel. This immediately reduces odor, prevents flies and limits bacteria and other pests. This step results in pre-dried manure with up to 45% dry matter.
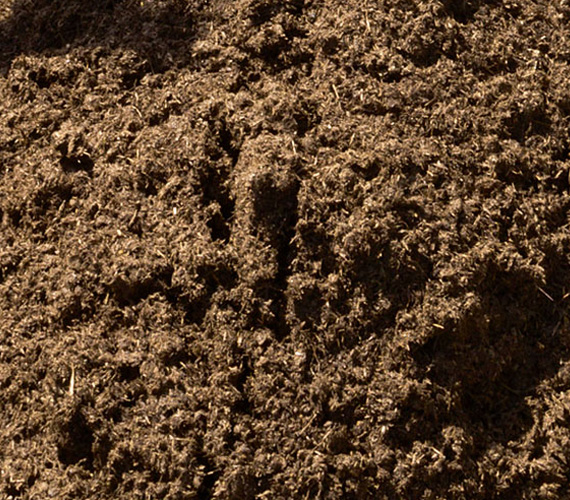
The second step uses oxygen in a composting process to turn the manure into organic fertilizer. The entire mixing process requires no heat supplement, since it generates heat itself thanks to the aerobic bacteria.
The third step produces pellets from the compost that are compact and easy to pack as high-quality, odorless organic fertilizer for plants and crops.
“Using this system, wet manure is removed from poultry sheds every two days. Farmers can invest step by step in the process, and grow in accordance with their generated income and financial capacity,” Mr Van Der Mark added.
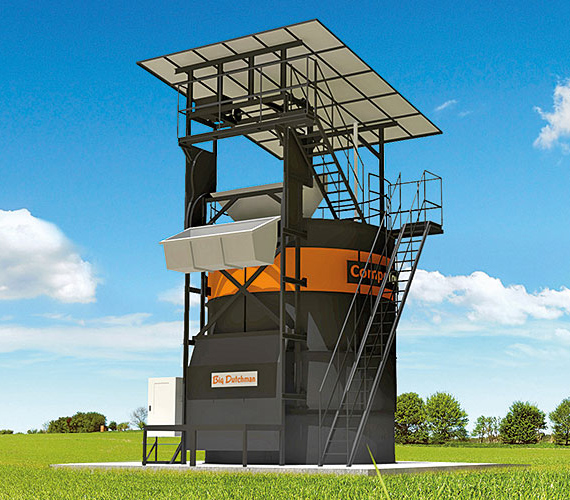
Sustainable solutions
By introducing more efficient production solutions, Big Dutchman says it is bringing sustainability to its business.
Zero waste
“With intensive livestock farming, the pressure on the environment increases and we need to introduce zero waste solutions. There is a lot of discussion on emissions reduction and carbon footprints. Farms are getting closer to communities, so odor treatment is a hot topic as well,” said Mr Van Der Mark.
“We have been seriously studying, investing in and developing solutions to alleviate the impact of livestock production on the environment and at the same time saving on energy use. In other words, our solutions bring about both environmental and economic benefits.”
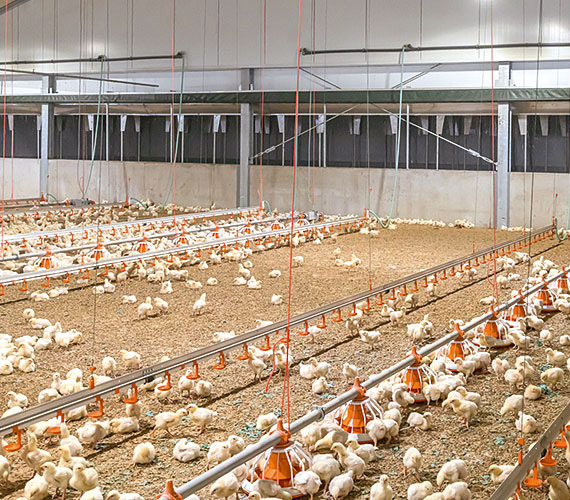
Air cleaning
Big Dutchman is also introducing air cleaning systems that reduce dust, clean the air and recondition heat from sheds into cool air. These can bring significant energy savings and other benefits to poultry and pig farms.
The company is also studying the use of recycled energy. In Vietnam, it is cooperating with solar panel suppliers to provide solar energy systems at broiler and layer farms. “We play a coordinating role linking the farmers with solar panel service suppliers,” said Mr Van Der Mark.
With limited financial resources, farmers tend to choose the systems that bring the fastest results at the cheapest price, he said. However, this often forces them to sacrifice other important factors of livestock production.
“Ventilation systems, premises and farm equipment are the three most important investment factors in livestock production. It is necessary to have all three because each affects the efficiency of the other and the final result as a whole. It’s a holistic concept,” he explained.
All aspects should be seen as potential profit centers and not cost centers. A decision to sacrifice one of these may have significant longterm effects on performance and thus revenue returns. Therefore, it is important to properly balance the investment.
“The optimal conditioning of livestock and creating the best atmosphere to maximize performance is priority. You do this by investing in the best climate and ventilation solutions, thereby assuring consistent conditions through your building, equipment and systems,” he added.